Mastering Arm Movements
Imagine a humanoid robot reaching out to shake your hand. It’s not just about extending an arm; it’s about mimicking the fluidity and precision of human motion. But how do they do it? How do humanoid robots achieve such realistic arm movements without looking like stiff, mechanical puppets?
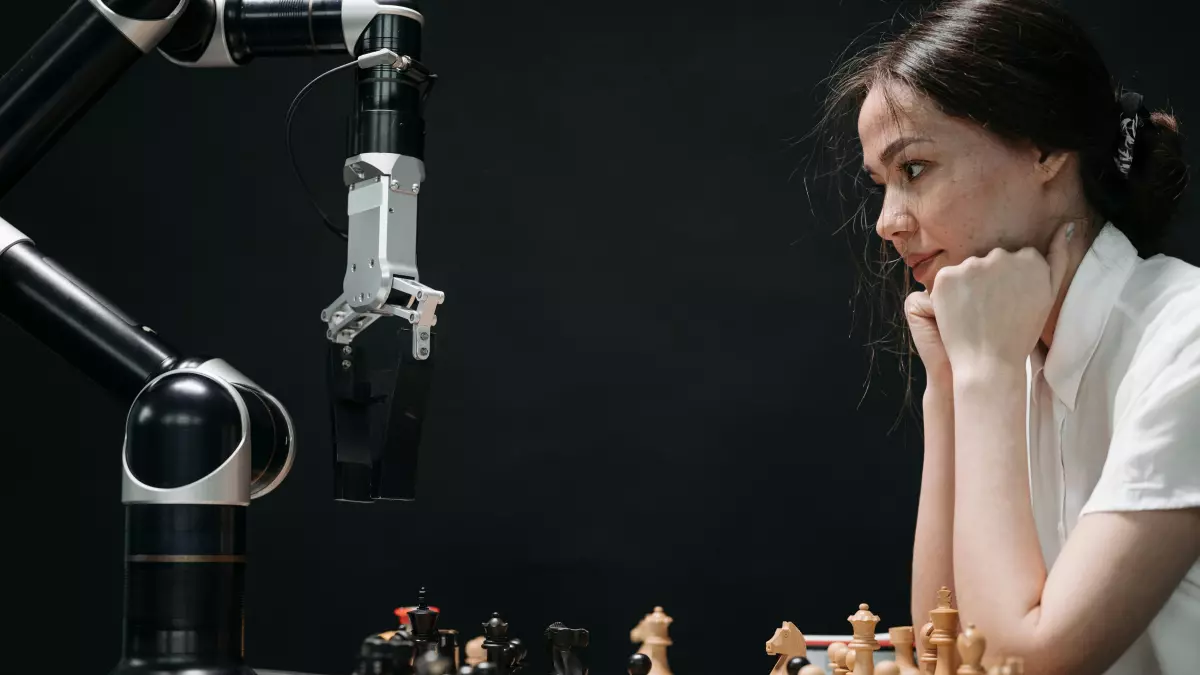
By Dylan Cooper
Let’s rewind to a robotics lab where engineers are faced with a challenge: designing a humanoid robot that can perform complex arm movements with the same grace and accuracy as a human. The stakes are high—after all, arms are one of the most versatile tools in the human body, capable of everything from lifting heavy objects to performing delicate tasks like threading a needle. The solution? A combination of sensor integration, motion control algorithms, and some seriously advanced engineering.
In this article, we’ll break down the science behind humanoid robot arm control, exploring how sensors, actuators, and algorithms come together to create lifelike movements. Whether you’re a robotics enthusiast or just curious about how these machines work, you’re in for a deep dive into the world of robotic arms.
The Role of Sensors: Eyes and Ears of the Robot
First things first: sensors. If you think about it, human arms don’t just move on their own. They rely on input from our senses—sight, touch, and even hearing—to adjust and adapt to the environment. Humanoid robots work the same way, but instead of biological senses, they use a network of sensors to gather data.
For arm control, the most important sensors are typically force sensors, position sensors, and proximity sensors. Force sensors help the robot understand how much pressure it’s applying when it grips something, preventing it from crushing a delicate object or failing to hold onto something heavy. Position sensors, on the other hand, track the exact location of the arm in space, ensuring that the robot knows where its hand is at all times. Proximity sensors allow the robot to detect objects nearby, helping it avoid collisions or adjust its path to reach a target.
These sensors work together to provide the robot with real-time feedback, allowing it to make split-second adjustments to its movements. Without them, the robot would be blind to its surroundings and unable to perform tasks with any degree of precision.
Motion Control Algorithms: The Brain Behind the Brawn
Now that the robot has sensory input, it needs to figure out how to use that information to move its arm. This is where motion control algorithms come in. Think of these algorithms as the robot’s brain—they process the data from the sensors and translate it into specific commands for the robot’s actuators (the mechanical parts that move the arm).
One of the most important types of algorithms used in humanoid robot arm control is the inverse kinematics algorithm. This algorithm helps the robot figure out how to move its joints to achieve a desired position for its hand. For example, if the robot wants to pick up a cup from a table, the inverse kinematics algorithm will calculate the exact angles and positions for each joint in the arm to make that happen.
But it’s not just about getting the hand to the right spot. The robot also needs to move smoothly and naturally, which is where trajectory planning algorithms come into play. These algorithms ensure that the arm moves in a fluid, continuous motion, rather than jerking from one position to another. This is crucial for tasks that require precision, like pouring a drink or assembling small parts.
Actuators: The Muscles of the Robot
Once the motion control algorithms have figured out how the arm should move, it’s time for the actuators to do their thing. Actuators are the mechanical components that actually move the robot’s joints. In humanoid robots, actuators are often designed to mimic the function of human muscles, providing both strength and flexibility.
There are several types of actuators used in humanoid robots, but the most common are electric motors and hydraulic actuators. Electric motors are great for precise, controlled movements, while hydraulic actuators are better suited for tasks that require a lot of force, like lifting heavy objects.
In some advanced humanoid robots, engineers are experimenting with artificial muscles—actuators made from materials that contract and expand like real muscles. These artificial muscles offer a more natural range of motion and could be the key to even more lifelike arm movements in the future.
Challenges and Future Directions
While humanoid robot arm control has come a long way, there are still plenty of challenges to overcome. One of the biggest hurdles is fine motor control—the ability to perform delicate tasks that require a high degree of precision. While robots can already perform tasks like gripping and lifting, they still struggle with more intricate movements, like threading a needle or tying a knot.
Another challenge is energy efficiency. Moving a robot’s arm requires a lot of power, especially for tasks that involve heavy lifting. Engineers are constantly working to make actuators more energy-efficient, but there’s still a long way to go before robots can match the endurance of human arms.
Despite these challenges, the future of humanoid robot arm control looks bright. Advances in artificial intelligence, machine learning, and materials science are paving the way for even more realistic and capable robotic arms. Who knows? In a few years, we might see robots performing surgery, playing musical instruments, or even competing in sports.
So, the next time you see a humanoid robot reaching out to shake your hand, remember: there’s a lot more going on behind the scenes than meets the eye. From sensors to algorithms to actuators, every movement is the result of years of research and engineering. And as technology continues to evolve, we’re only scratching the surface of what these robots can do.
In the end, it’s not just about building a robot that can move its arm—it’s about building a robot that can move like us.