Sensors & Actuators
I remember the first time I saw a robot arm in action at a tech expo. It was mesmerizing—this mechanical arm was picking up objects with such precision, it almost seemed human. But what really blew my mind was learning that behind this fluid motion were two unsung heroes: sensors and actuators. These components work together to make robots move, think, and react. And yet, they often don’t get the spotlight they deserve.
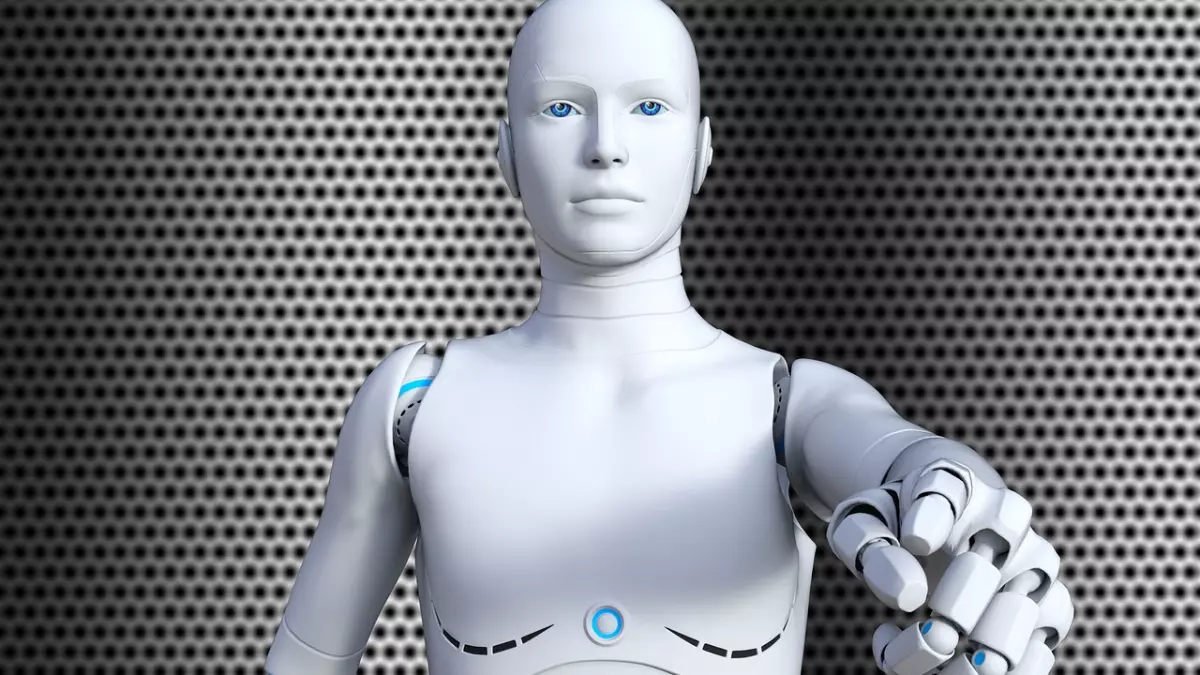
By Tomás Oliveira
When we talk about robotics, it’s easy to get caught up in the flashy stuff—AI, machine learning, or even the robot’s sleek design. But at the core of every robot’s functionality lie two crucial components: sensors and actuators. These are the building blocks that allow robots to perceive their environment and interact with it. Without them, robots would be nothing more than fancy paperweights.
So, let’s break it down. What are sensors and actuators, and why are they so important? Sensors are the robot’s way of gathering information about the world. They can detect things like light, temperature, pressure, and even proximity. Actuators, on the other hand, are the muscles of the robot. They take the information from the sensors and translate it into movement or action. Together, these two components form the backbone of any autonomous system.
How Sensors Work in Robotics
Sensors are essentially the robot’s eyes, ears, and skin. They provide the raw data that the robot’s control system uses to make decisions. There are many different types of sensors, each designed to detect specific environmental factors. For example, vision sensors use cameras to capture images or video, allowing the robot to “see” its surroundings. Proximity sensors help robots avoid obstacles by detecting how close they are to objects.
Another key type of sensor is the force sensor, which measures the amount of force being applied to an object. This is especially important in tasks like gripping, where too much or too little force could result in failure. Temperature sensors are also crucial in environments where heat could damage the robot or its components. And let’s not forget gyroscopes and accelerometers, which help robots maintain balance and orientation.
But sensors alone aren’t enough. They provide the data, but that data needs to be processed and acted upon. That’s where actuators come in.
The Role of Actuators in Robotics
If sensors are the eyes and ears, actuators are the muscles. They convert electrical signals into physical movement. There are several types of actuators, each suited for different tasks. The most common types are electric motors, hydraulic actuators, and pneumatic actuators.
Electric motors are the most widely used actuators in robotics. They’re efficient, reliable, and can be easily controlled. You’ll find them in everything from robot arms to autonomous vehicles. Hydraulic actuators, on the other hand, are used when more power is needed. They use pressurized fluid to create movement and are often found in heavy-duty robots, like those used in construction or manufacturing. Pneumatic actuators work similarly but use compressed air instead of fluid. They’re typically used for lighter tasks where precision isn’t as critical.
Actuators are responsible for all the physical actions a robot performs. Whether it’s moving a robotic arm, driving a wheel, or even opening a door, actuators make it happen. But they don’t act alone—they rely on the data provided by sensors to know what to do and when to do it.
The Sensor-Actuator Feedback Loop
The real magic happens when sensors and actuators work together in a feedback loop. Here’s how it works: the sensors gather data from the environment, which is then processed by the robot’s control system. Based on that data, the control system sends signals to the actuators, telling them how to move. The actuators then perform the action, and the sensors monitor the results to ensure everything is going as planned.
This feedback loop is what allows robots to adapt to changing environments and perform complex tasks with precision. For example, in a robotic arm, sensors might detect the position of an object, while actuators move the arm to pick it up. If the sensors detect that the arm is off-target, they send new data to the control system, which adjusts the actuators’ movements accordingly.
In more advanced systems, this feedback loop can happen in real-time, allowing robots to make split-second decisions and adjustments. This is especially important in autonomous robots, which need to navigate unpredictable environments without human intervention.
Challenges in Sensor and Actuator Integration
While sensors and actuators are essential, integrating them into a cohesive system is no easy task. One of the biggest challenges is latency. The time it takes for data to travel from the sensors to the control system and then to the actuators can affect the robot’s performance. In high-speed applications, even a slight delay can result in errors or accidents.
Another challenge is accuracy. Sensors need to provide precise data, and actuators need to execute movements with pinpoint accuracy. Any deviation can lead to failure, especially in tasks that require a high degree of precision, like surgery or assembly line work.
Finally, there’s the issue of power consumption. Both sensors and actuators require energy to function, and in mobile robots, power is often limited. Engineers need to find ways to optimize power usage without sacrificing performance.
The Future of Sensors and Actuators in Robotics
As technology advances, so do sensors and actuators. We’re already seeing the development of smart sensors that can process data on their own, reducing the load on the control system. Soft actuators, made from flexible materials, are also becoming more common, allowing robots to perform more delicate tasks.
In the future, we can expect sensors and actuators to become even more integrated, working together seamlessly to create robots that are faster, more precise, and more autonomous than ever before. Imagine a world where robots can perform complex surgeries, build skyscrapers, or even explore other planets—all thanks to the humble sensor and actuator.
So, the next time you see a robot in action, remember that behind every smooth movement and precise action are sensors and actuators working in perfect harmony. They may not be as flashy as AI or machine learning, but without them, robots wouldn’t be able to do much of anything.
I still think back to that robot arm at the tech expo. It was a simple demonstration, but it opened my eyes to the incredible complexity behind every robotic movement. And now, every time I see a robot in action, I can’t help but appreciate the sensors and actuators making it all possible.