Designing Autonomous Sensors
Think you can just slap a sensor on a robot and call it a day? Not so fast. Many people believe that sensors are just plug-and-play components in robotics, but the reality is far more complex. Designing sensors for autonomous robots is a delicate dance between hardware, software, and control systems.
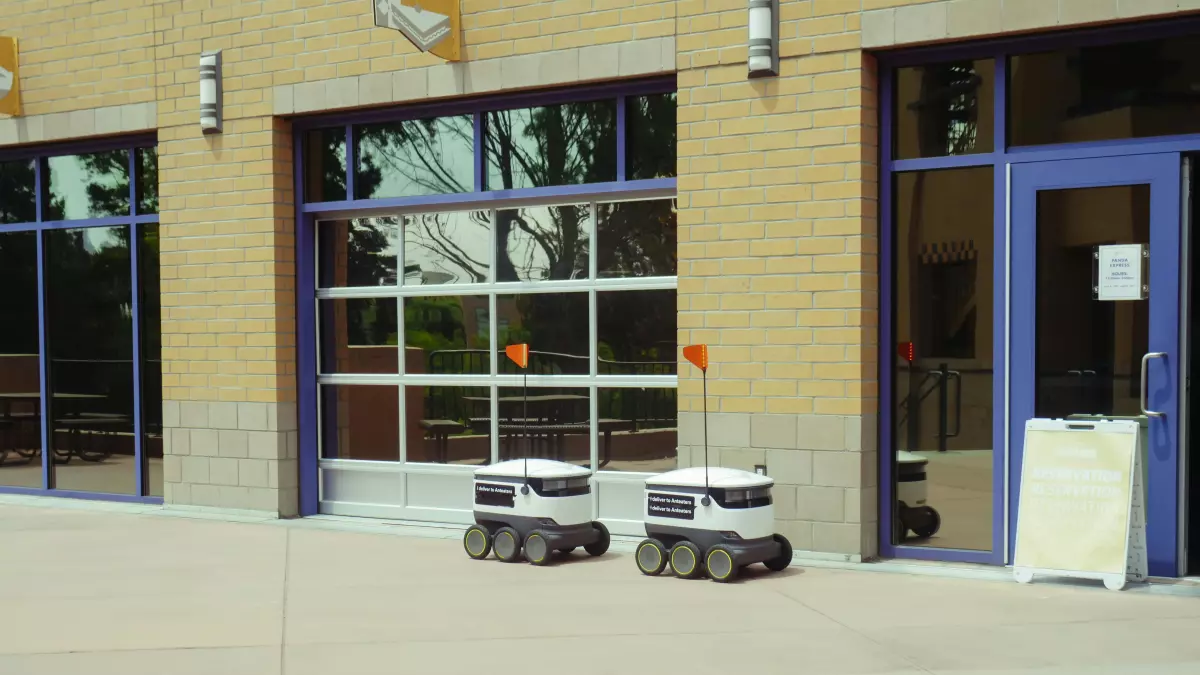
By Kevin Lee
Here’s the thing: sensors are not just passive components that gather data. They are the eyes, ears, and sometimes even the 'skin' of a robot. Without them, robots would be like humans walking around blindfolded, unable to interact with their environment. But designing these sensors is no easy task. It requires a deep understanding of both the physical world and the digital systems that interpret it.
So, how do you go about designing sensors for autonomous robots? Let's break it down into five crucial steps that will help you understand the process from start to finish.
1. Define the Robot's Purpose
Before you even think about the hardware, you need to ask yourself: What is the robot supposed to do? Is it navigating through a warehouse, picking up objects, or maybe even exploring Mars? The robot’s purpose will dictate the types of sensors you’ll need. For example, a robot navigating indoors might rely heavily on LiDAR or cameras, while an outdoor robot might need GPS and environmental sensors.
Once you’ve defined the robot’s purpose, you can start narrowing down the types of sensors that will be necessary. This is where you’ll decide whether you need proximity sensors, temperature sensors, cameras, or something more specialized like a spectrometer.
2. Choose the Right Hardware
Now that you know what your robot needs to sense, it's time to pick the right hardware. This is where things can get tricky. You need to balance cost, size, and power consumption. For example, a high-resolution camera might give you excellent data, but it could also drain your robot’s battery faster than you can say 'shutdown.'
Another factor to consider is the environment. Will the robot be operating in extreme temperatures or under water? If so, you’ll need sensors that can withstand those conditions. Durability is key here. You don’t want your robot to fail because a sensor shorted out in the rain.
3. Integrate with Control Systems
Once you’ve chosen your hardware, the next step is to integrate the sensors with the robot’s control systems. This is where the magic happens. The data from the sensors needs to be processed and interpreted by the robot’s 'brain,' which is usually a combination of microcontrollers, processors, and software algorithms.
But here’s the catch: not all sensors speak the same language. Some might output analog signals, while others send digital data. You’ll need to ensure that your control system can handle these different types of inputs. This often involves using converters or signal processors to get everything working together smoothly.
4. Develop the Software
Hardware is only half the battle. You also need software that can make sense of the data coming from the sensors. This is where algorithms come into play. Your software needs to filter out noise, make sense of incomplete data, and sometimes even predict what the robot should do next based on the sensor inputs.
For example, a robot navigating through a cluttered environment might use a combination of LiDAR and camera data to build a 3D map of its surroundings. The software would then use this map to plan the robot’s path, avoiding obstacles and finding the most efficient route.
Machine learning can also play a role here. By training the robot on large datasets, you can improve its ability to interpret sensor data in real-time, making it more autonomous and capable of handling complex tasks.
5. Test and Calibrate
Finally, no sensor system is complete without rigorous testing and calibration. This is where you make sure that the sensors are actually doing what they’re supposed to do. You’ll need to test the robot in different environments and under various conditions to ensure that the sensors are reliable.
Calibration is also crucial. Over time, sensors can drift, meaning their readings become less accurate. Regular calibration ensures that the robot continues to perform at its best, even as its sensors age.
In some cases, you might even need to develop custom calibration routines, especially if you’re using specialized sensors that don’t have off-the-shelf calibration tools available.
What’s Next for Autonomous Sensors?
As robots become more advanced, so too will their sensors. We’re already seeing the rise of 'smart' sensors that can process data on the fly, reducing the load on the robot’s central processor. In the future, we might even see sensors that can adapt to their environment, changing their sensitivity or focus based on the task at hand.
Another exciting development is the integration of AI directly into sensor systems. Imagine a camera that not only captures images but also identifies objects and makes decisions about what the robot should do next. This kind of sensor fusion could revolutionize the way robots interact with the world.
So, while designing sensors for autonomous robots is no easy task, it’s also an incredibly rewarding one. The sensors you choose and the way you integrate them will ultimately determine how well your robot can navigate, interact with, and understand its environment. And as technology continues to evolve, the possibilities are endless.