Control Loops
Imagine a robot arm trying to pick up a delicate object, but instead of smoothly grasping it, the arm jerks, overshoots, and crushes the object. What went wrong? The answer lies in the control loop—or rather, the lack of a good one.
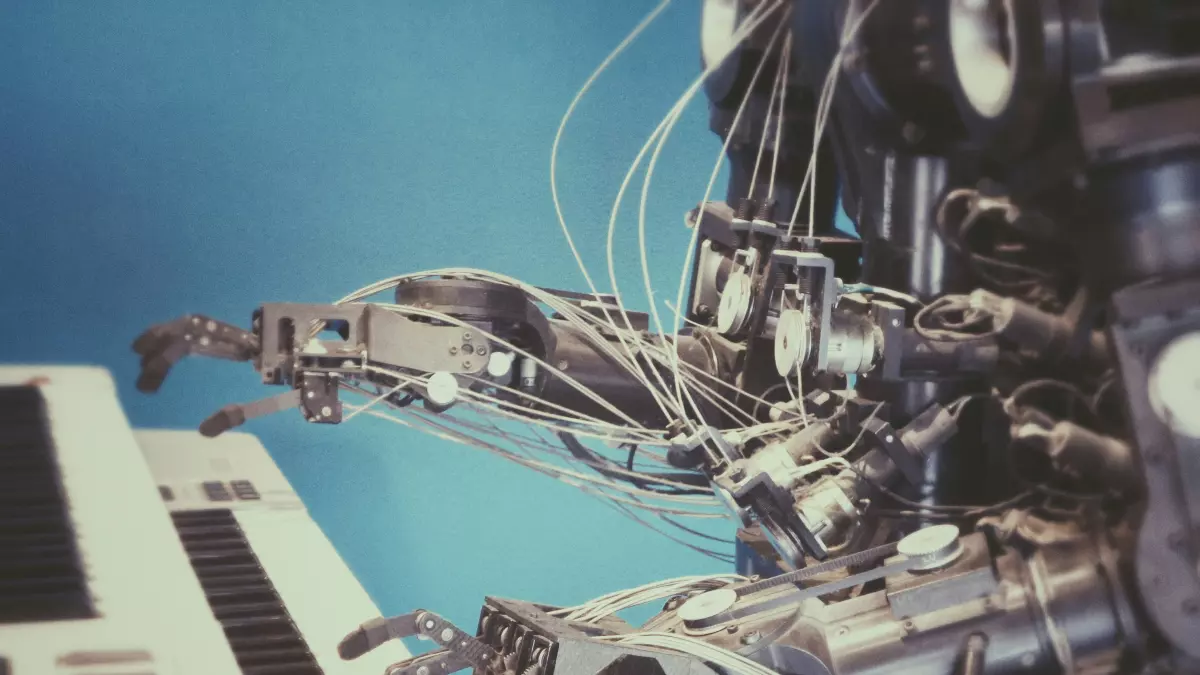
By Sarah Kim
Control loops are the unsung heroes of robotics. They are the invisible force that ensures robots don’t just move, but move with precision, efficiency, and purpose. Whether it’s a robotic arm assembling a car or a drone flying through a crowded city, control loops are what keep everything in check. But what exactly are they, and why are they so crucial?
Let’s break it down. A control loop is essentially a feedback mechanism that helps a robot adjust its actions in real-time. It’s like when you’re driving a car and constantly adjusting the steering wheel to stay in your lane. You’re receiving feedback from the road (through your eyes and hands) and making tiny corrections to keep things smooth. Robots do something similar, but instead of eyes and hands, they use sensors and actuators.
How Control Loops Work
At the heart of every control loop is a simple concept: feedback. The robot performs an action, measures the result, compares it to the desired outcome, and then adjusts accordingly. This process repeats continuously, sometimes thousands of times per second, depending on the task.
Here’s a basic breakdown of how it works:
- Sensors: These gather data from the environment. For example, a robot arm might have sensors that measure its position, speed, and force.
- Controller: This is the brain of the loop. It takes the sensor data and compares it to the desired outcome (e.g., the arm should be at position X with speed Y).
- Actuators: These are the muscles of the robot. Based on the controller’s instructions, they adjust the robot’s movements to correct any errors.
- Feedback: The sensors continuously send updated information back to the controller, which keeps adjusting the actuators. And the loop goes on.
This constant cycle of sensing, comparing, and adjusting is what allows robots to perform complex tasks with precision. But not all control loops are created equal. There are different types, each suited for different tasks.
Types of Control Loops
There are two main types of control loops in robotics: open-loop and closed-loop systems.
- Open-Loop Systems: These are the simplest form of control. The robot performs an action without any feedback. Imagine throwing a dart at a target while blindfolded. You have no idea if you hit the bullseye or missed entirely. Open-loop systems are fast but not very accurate. They’re used in situations where precision isn’t critical, like turning on a motor for a set amount of time.
- Closed-Loop Systems: These are the more advanced and commonly used systems. They rely on feedback to adjust the robot’s actions in real-time. It’s like throwing a dart with your eyes open and making tiny adjustments based on where the dart is heading. Closed-loop systems are essential for tasks that require high precision, like robotic surgery or autonomous driving.
Most modern robots rely on closed-loop systems because they offer the best balance of speed and accuracy. But even within closed-loop systems, there are different levels of complexity.
PID Control: The Gold Standard
One of the most common types of closed-loop control is PID control, which stands for Proportional, Integral, and Derivative. It sounds fancy, but it’s basically a way to fine-tune how a robot responds to errors.
Here’s how it works:
- Proportional: This part of the control system makes adjustments based on how far off the robot is from the target. The bigger the error, the bigger the correction.
- Integral: This part looks at the accumulated error over time. If the robot keeps missing the target, the integral part will increase the correction to compensate.
- Derivative: This part predicts future errors based on the current rate of change. It helps the robot anticipate and smooth out its movements.
When combined, these three elements allow robots to make incredibly precise adjustments, whether they’re balancing on two legs or threading a needle.
Why Control Loops Matter
Without control loops, robots would be clumsy, inefficient, and downright dangerous. Imagine a self-driving car that couldn’t adjust its speed based on traffic or a robotic arm that couldn’t stop itself from crushing delicate objects. Control loops are what make robots safe, reliable, and capable of performing tasks that humans can’t.
As robots become more advanced, control loops will only become more important. With the rise of AI and machine learning, we’re starting to see control loops that can adapt and learn from their mistakes, making robots even more autonomous and efficient.
So, the next time you see a robot performing a task with incredible precision, remember that behind the scenes, there’s a control loop working tirelessly to make it all happen.
And who knows? Maybe one day, we’ll have control loops so advanced that robots will be able to adjust to any situation without breaking a sweat—or a circuit.