Safety First
Imagine a world where robots work seamlessly alongside humans without a single mishap. That’s the dream, right? But how do we get there?
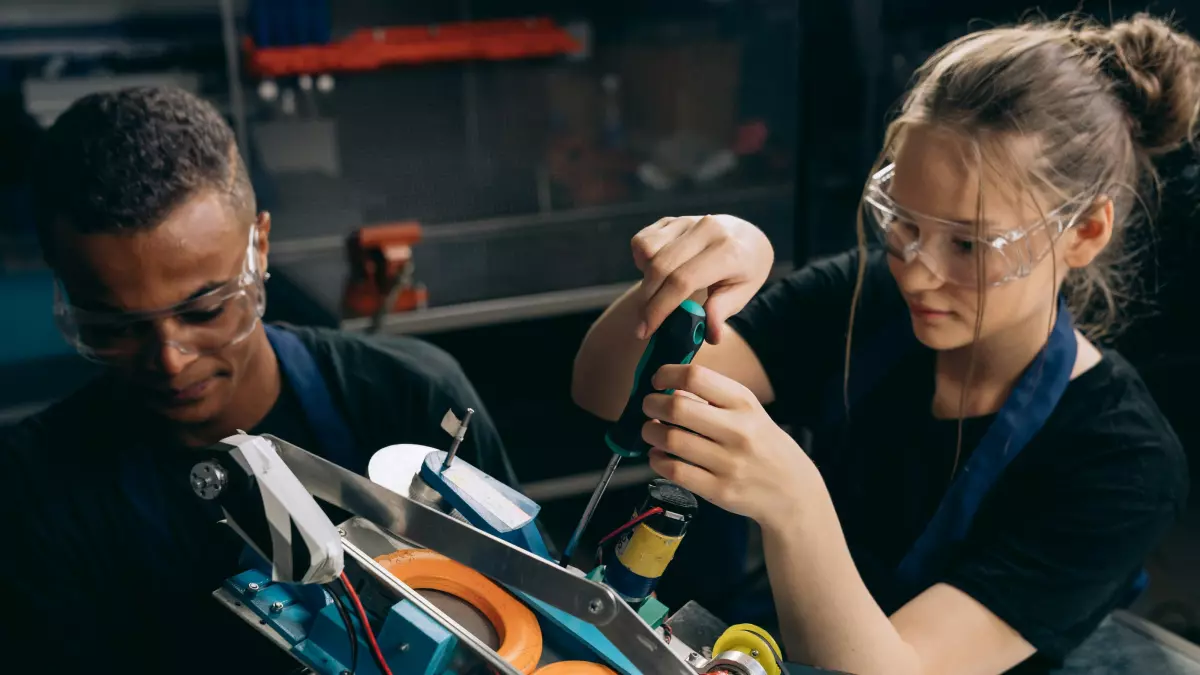
By James Sullivan
Enter robot safety systems. These are the unsung heroes of robotics, ensuring that autonomous machines don’t just operate efficiently but also safely. While we often marvel at a robot’s ability to perform complex tasks, it’s the safety mechanisms humming quietly in the background that make these feats possible in the real world.
Why does this matter? Well, as robots increasingly integrate into industries like healthcare, manufacturing, and even our homes, the stakes are higher than ever. A single malfunction could lead to catastrophic consequences, not just for the robot but for the humans around it. This is where advanced safety systems come into play, acting as the invisible shield between innovation and chaos.
What Exactly Are Robot Safety Systems?
At their core, robot safety systems are a combination of hardware and software designed to prevent accidents. Think of them as the airbags and seatbelts of the robotics world. These systems include sensors, control algorithms, and fail-safe mechanisms that work together to detect, predict, and mitigate risks.
For instance, proximity sensors can detect when a human is too close to a robot’s operational zone, triggering an automatic stop. Similarly, force-torque sensors can ensure that a robot doesn’t apply excessive pressure during tasks like assembly or surgery. And let’s not forget about emergency stop buttons—simple yet effective tools that allow humans to take control instantly.
The Software Behind the Scenes
While hardware gets a lot of attention, the software driving these safety systems is equally critical. Advanced algorithms analyze data from sensors in real-time, making split-second decisions to avoid potential hazards. Machine learning is increasingly being used to improve these algorithms, enabling robots to learn from past incidents and adapt to new environments.
Take, for example, collaborative robots (or cobots). These robots are designed to work alongside humans, often in unpredictable settings. Their safety systems rely heavily on software to ensure that they can adapt to human movements and intentions without causing harm. This involves complex computations that balance speed, precision, and safety—a trifecta that’s easier said than done.
Standards and Regulations
Now, you might be wondering: who decides what’s "safe" for a robot? Enter organizations like the International Organization for Standardization (ISO) and the Robotics Industries Association (RIA). These bodies establish guidelines and standards that manufacturers must adhere to, such as ISO 10218 for industrial robots and ISO/TS 15066 for collaborative robots.
Compliance with these standards isn’t just a legal requirement; it’s a trust-building exercise. When a robot meets these stringent criteria, it signals to users that the machine is reliable and safe to operate. This is especially crucial in sectors like healthcare, where lives are literally on the line.
Challenges in Implementing Safety Systems
Of course, no system is perfect. One of the biggest challenges in robot safety is the trade-off between functionality and security. Adding too many safety features can slow down a robot’s performance, making it less efficient. On the flip side, prioritizing speed and efficiency can compromise safety.
Another hurdle is cost. Advanced safety systems aren’t cheap, and not all companies can afford to implement them. This creates a disparity where only well-funded organizations can deploy the safest robots, leaving smaller players at a disadvantage.
The Future of Robot Safety
So, what’s next? The future of robot safety lies in predictive systems. These are systems that don’t just react to risks but anticipate them. Using technologies like AI and IoT, robots will soon be able to predict potential hazards based on patterns and trends, taking preemptive actions to avoid them.
Imagine a robot in a warehouse that can predict when a shelf is about to collapse based on vibrations and weight distribution. Or a surgical robot that can anticipate a surgeon’s next move, ensuring that its tools are always in the right position. These aren’t just sci-fi fantasies; they’re the next frontier in robotics.
Moreover, as robots become more interconnected, we’ll see the rise of networked safety systems. These systems will allow robots to share safety data with each other, creating a collaborative safety net that benefits everyone.
Wrapping It Up
Robot safety systems may not be the flashiest aspect of robotics, but they’re undoubtedly one of the most important. As we continue to push the boundaries of what robots can do, ensuring their safety—and ours—will remain a top priority.
So, the next time you marvel at a robot performing a seemingly impossible task, take a moment to appreciate the safety systems working tirelessly behind the scenes. After all, innovation without safety is like driving a sports car without brakes—exciting but ultimately disastrous.